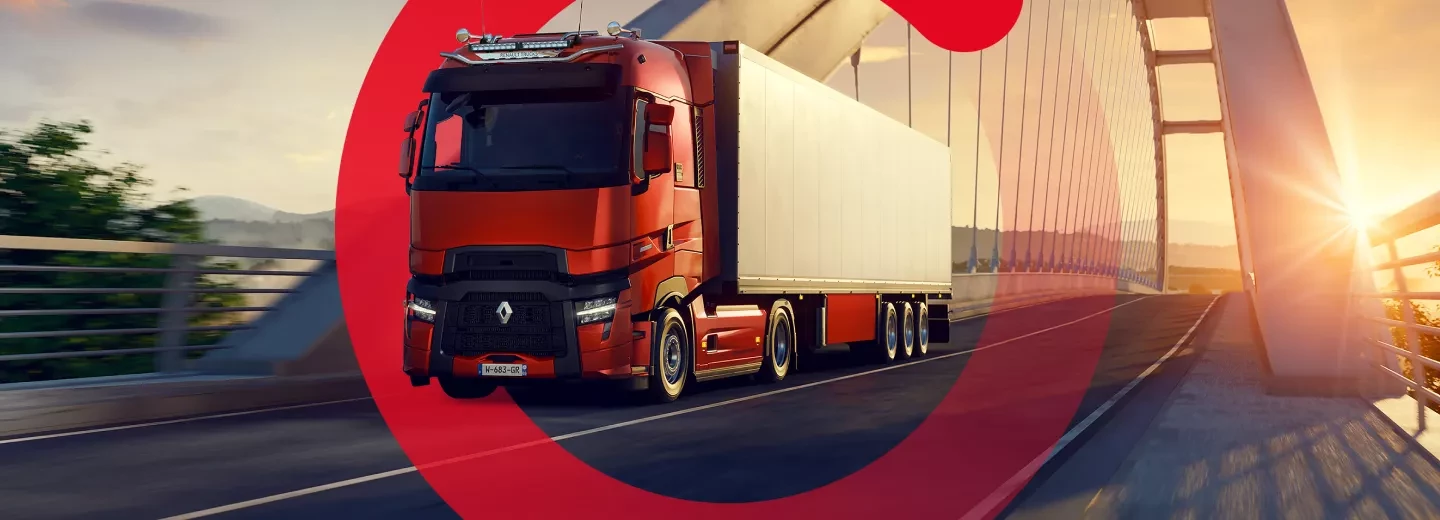
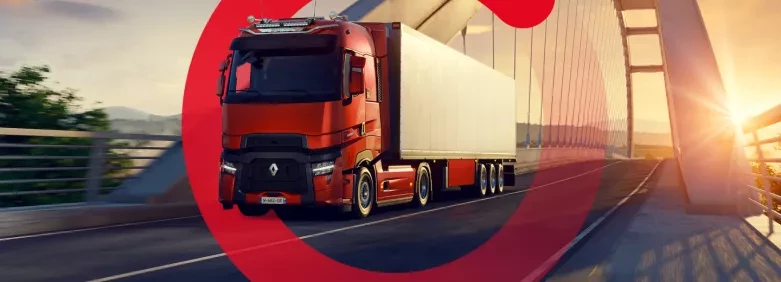
28 August 2025
The circular economy: Renault Trucks’ approach to the environmental challenge
Given the urgent need to leave behind the productivist economic model, now untenable for the environment and human society, Renault Trucks has chosen a new avenue for its trucks: the circular economy.
Faced with the threefold challenge of achieving carbon neutrality, protecting natural resources and overcoming the shortage of industrial components, the circular economy is no doubt the best response.
Every facet of our business is affected by circularity. It prompts us to factor in the environmental impact of our operations and rethink our approach to designing and manufacturing products, our knowledge of the value chain, but also our development of business models and our ability to bring our customers added value.
Our action is underpinned by three pillars: regenerate, repurpose, and return. Our objective is clear: to prolong the value of our trucks and parts for as long as possible, with the same guarantees of quality and cost-effectiveness as for new products.
The circular economy at Renault Trucks: images and figures to prove it
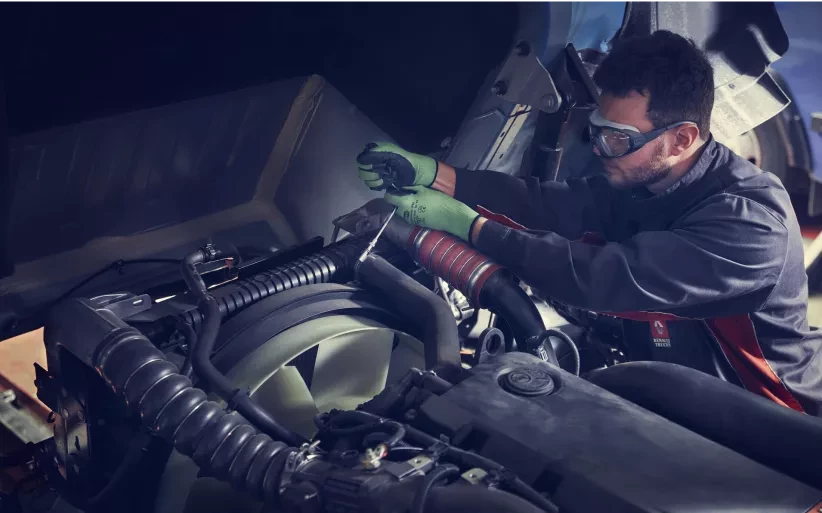
The circular economy: achievements and outlook
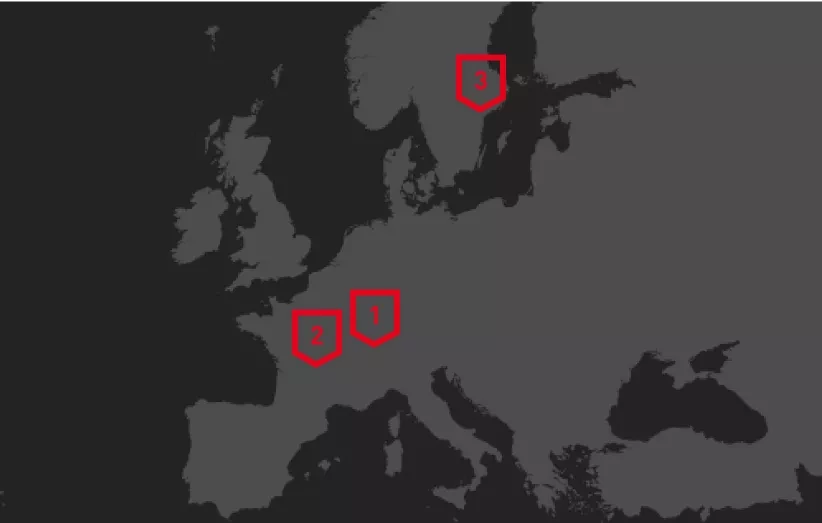
Learn more about our dedicated circular-economy plants
1- Bourg-en-Bresse, France
Our plant specialized in converting used trucks
2- Limoges, France
Our plant specialized in renovating mechanical components
3- Flen, Sweden
Our plant specialized in renovating engine components
-85%
Our REMAN parts range saves up to 85% on raw materials.
95%
Recycling: our trucks are 95% recyclable and over 98% recoverable
(according to the ISO 22628 standard)
Under 7.7 tonnes
A regenerated Renault Trucks vehicle saves up to 7.7 tonnes of CO2 by comparison with an equivalent new truck.
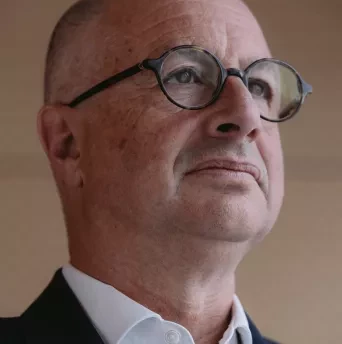
Frugality is a necessity : We are convinced that another path is possible, one of 'strictly necessary', which involves responding strictly to needs - neither more nor less - in our consumption and in what we offer to our customers. To effectively act towards the decarbonization of transportation, this approach is inseparable from the circular economic model.
Our commitments for 2030
30%
of spare parts sales revenue will come from reused parts
1,200 Renault trucks
regenerated or repurposed Renault Trucks put back on the road by our customers
Questions & Answers
We at Renault Trucks fully endorse the definition and principles laid down by the Ellen MacArthur Foundation:
“In our current economy, we take materials from the Earth, make products from them, and eventually throw them away as waste – the process is linear. In a circular economy, by contrast, we stop waste being produced in the first place. A circular economy is based on three principles, all driven by design: eliminate waste and pollution, circulate products and materials (at their highest value), regenerate nature. Underpinned by a transition to renewable energy and materials, the circular economy is a resilient system that is good for business, people, and the environment.”
Instead of using the planet’s resources to build new trucks and spare parts, in 2019 we adopted a circular approach in which we are continually progressing. We have set up solutions to extend the useful life of our own trucks so that our customers can keep them for longer.
Our first step was to regenerate used trucks to give them a second life. This led us to set up the Used Truck Factory, which regenerates and repurposes trucks to meet market demands. Since 2019, we have been marketing a range of reconditioned trucks under our own brand.
We then undertook to combat obsolescence and extend our trucks’ first lifetime so that they can be used intensively for longer by their initial owners. The regenerated trucks range is geared towards customers with large fleets who, instead of replacing their vehicles, opt instead for reconditioning. Their trucks are appraised, the cab interior is redesigned, and we work on the kinematic chain, updating the vehicle with the latest software (in particular to track consumption and the performances with regard to CO2 emissions). That way, we can offer our customers their own freshly-renovated trucks rather than selling them new vehicles, in keeping with our “lean” approach.
This circular approach also applies to our spare parts. We have decided to develop the regeneration and reuse of spare parts and components. Up until now, our Limoges factory was the only site specialised in remanufacturing major truck parts (gearboxes, engines, etc.). We are currently building a truck dismantling plant to recover and recycle - once cleaned and regenerated - all parts that have a strong potential for reuse.
By perpetually regenerating, converting and reusing our trucks and by reconditioning our parts, we are adding new value, extending their lifespan and keeping them constantly on the move. Because Trucks are forever !
Innovation is not a race for novelty. For Renault Trucks, the main goal is to design ingenious, effective and sustainable solutions that preserve natural resources and reduce our greenhouse gas emissions. By challenging our production models and our offers, innovation aims to foster the emergence of concrete ideas to continue meeting our customers’ needs while at the same time reducing our impact.
When we extend trucks’ lifespan, we save 7.7 tonnes of CO2 for each regenerated truck. To calculate this figure, we look at the minerals we would have had to mine, the parts we would have had to produce and the manufacturing operations we would have had to carry out to produce a new vehicle.
Products and materials must be used for as long as possible. The term regenerate refers to the solutions we have set up to extend our own trucks’ lifespan so that our customers can keep them for longer. Longer life cycles help reduce the resources used, reduce the carbon footprint and minimise the environmental impact. By choosing to regenerate the trucks bearing our brand in our customers’ fleet and to use them for longer, we avoid producing new vehicles, which in turn reduces demand for the natural resources and energy required to make them.
Vehicle regeneration supports the circular economy in a variety of ways:
Reuse of resources: regenerating a used vehicle generally means repairing or replacing faulty or worn parts instead of discarding them or replacing them with new parts. This extends the vehicle’s useful life and avoids the need to consume new resources to manufacture new parts, thereby reducing demand for the raw materials and energy needed to produce them.
Waste reduction: The regeneration of a used vehicle, by preventing the vehicle from being scrapped or destroyed, reduces the amount of waste involved in the automobile industry. Recovered used vehicles are refurbished and put back on the market, thereby preventing them from adding to the waste that is proving such a burden for our society.
Reduction of the carbon footprint: Producing new vehicles has a major environmental impact because of the greenhouse gas emissions entailed in the production, transport and processing of the materials. By remanufacturing used vehicles, we avoid the production of new vehicles and reduce their impact on greenhouse gas emissions.
Cost reductions: conversion can prove cheaper than buying a new vehicle, ever though that depends on the type of vehicle and the complexity of the conversion.
Reduced carbon footprint: by converting an existing vehicle, we avoid the production of a new vehicle and reduce its impact on greenhouse gas emissions.
Customisation: vehicle conversions are also an opportunity to personalize the vehicle to suit the owner’s needs and tastes. Customisation options might include the choice of battery power, vehicle range and engine configuration.
Potential job creation: Converting vehicles can also create job opportunities for people with skills in mechanics or manufacturing. That can boost the local economy and provide well-paid jobs in the industry.
Broken parts are often regarded as waste, but at Renault Trucks, we see them as an opportunity. Through our Remanufacturing programme, the damaged parts collected in our repair network are given a second life through a rigorous industrial process.
Once removed, cleaned, inspected, reconditioned, reassembled and fully tested, our parts have all of their original characteristics and performances. They are then reinjected onto the spare-parts market, ready to cover hundreds of thousands more kilometres.
Giving a second life to our parts has a significant effect on the environment by comparison with the purchase of a new part. It takes up to 85% less raw materials and 80% less energy to remanufacture parts. In 2022, all of the Remanufactured parts used in our repair network saved a combined total of over 1,900 tonnes of CO2: that’s the equivalent of the CO2 emissions generated by a high-speed train travelling 800,000 kms.
Our trucks are 95% recyclable and 98% recoverable, in accordance with the ISO 22628 standard. Each part is marked to facilitate its return to the appropriate recycling centre. Parts covered by the European Union’s REACH legislation on the production and use of chemical substances are systematically recorded and reported to the appropriate bodies.
It is thanks to this comprehensive process and the numerous practical steps taken to achieve our ambitions that we have become a standard-setter in the circular approach to the commercial vehicle offering and that we are consolidating our leadership in the transition to sustainable transport.